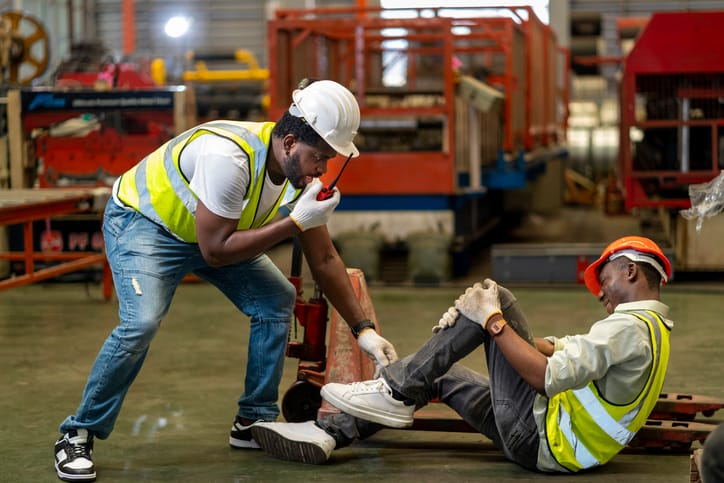
Workplace injuries happen across all industries, from offices to construction sites. Some injuries result from momentary lapses in attention, while others develop over time due to repetitive actions or exposure to hazards. Employers have a duty to reduce risks, but employees should also take precautions to protect themselves. Here, we outline ten common workplace injuries and practical steps to prevent them.
Slips, Trips and Falls
Slips, trips and falls are some of the most common workplace accidents and can happen in almost any environment. They often result from wet or uneven floors, cluttered walkways, loose cables, or poor lighting. In more hazardous settings, such as construction sites, falls from height pose an even greater risk, leading to serious injuries.
How to avoid them:
Keep floors clean and dry, addressing spills immediately
Use anti-slip mats in areas prone to wet conditions
Ensure walkways are clear of obstacles and secure loose cables
Improve lighting in dimly lit areas, particularly stairwells and corridors
Use handrails on stairs and maintain three points of contact when using ladders
Provide appropriate footwear with slip-resistant soles for employees working in environments with a high risk of slips
Conduct regular inspections to identify and rectify potential trip hazards
Muscle Strains
Muscle strains occur when muscles are overstretched or torn, often due to improper lifting techniques, poor posture or repetitive movements. These injuries are particularly common in jobs that require heavy lifting, carrying, or pulling loads, but they can also result from long periods of desk work in an awkward position.
How to avoid them:
Train workers on proper lifting techniques, bending at the knees and keeping loads close to the body
Avoid twisting while lifting or carrying heavy objects
Use mechanical aids such as trolleys or lifting equipment when available
Arrange workspaces ergonomically to reduce strain, ensuring desks, chairs and screens are set up correctly
Take regular breaks and incorporate stretching exercises into daily routines
Rotate tasks to reduce repetitive movements and give muscles time to recover
Impact injuries
Impact injuries occur when workers are struck by moving objects, such as tools, equipment or vehicles, or when objects fall from height. These accidents can cause bruising, fractures or even head injuries, depending on the force of the impact. Warehouses, construction sites and factories are particularly high-risk environments for these types of injuries.
How to avoid them:
Store items securely at height and ensure shelving is stable
Wear appropriate PPE, such as hard hats and steel-toe boots, when working in areas where objects may fall
Maintain clear walkways to prevent accidental collisions
Keep a safe distance from moving machinery and vehicles
Use safety barriers and warning signs in high-risk zones
Train employees on safe handling and storage of heavy tools and materials
Repetitive Strain Injury (RSI)
Repetitive strain injury (RSI) develops over time due to repeated motions, awkward postures, or prolonged use of tools, keyboards or machinery. It commonly affects the hands, wrists, shoulders and neck, leading to pain, stiffness and reduced mobility. Office workers, assembly line workers, and those using vibrating tools are particularly at risk.
How to avoid it:
Adjust workstations to promote good posture, ensuring chairs and desks are set at the right height.
Use ergonomic equipment, such as supportive chairs, wrist rests and adjustable keyboards.
Take regular breaks to stretch and rest affected muscles.
Rotate tasks where possible to avoid overuse of specific muscle groups.
Train employees on proper posture and hand positioning when using equipment.
Encourage light exercises to strengthen muscles and improve circulation.
Cuts and Lacerations
Sharp tools, machinery, and broken glass or metal edges can cause cuts and lacerations. These injuries can range from minor nicks to deep wounds that require medical attention. They are particularly common in industries such as construction, manufacturing and food preparation.
How to avoid them:
Use appropriate personal protective equipment (PPE), such as cut-resistant gloves.
Keep cutting tools sharp, as dull blades require more force and increase the risk of slips.
Store knives, box cutters and other sharp objects in designated areas when not in use.
Train employees on safe handling techniques for sharp tools and equipment.
Ensure machine guards are in place and functioning correctly to prevent accidental contact.
Dispose of broken glass or sharp objects safely in designated containers.
Inhalation Hazards
Exposure to airborne contaminants such as dust, fumes or chemicals can lead to respiratory issues. Workers in construction, manufacturing, laboratories, and cleaning industries face higher risks, particularly if ventilation is inadequate. Long-term exposure can contribute to conditions such as asthma, lung disease or even chemical poisoning.
How to avoid them:
Install and maintain proper ventilation systems to remove airborne contaminants.
Use respiratory protective equipment, such as masks or respirators, when working with hazardous substances.
Follow safety procedures for storing and handling chemicals to minimise exposure.
Train employees on recognising and managing inhalation risks.
Conduct regular air quality checks in workplaces where exposure risks are high.
Substitute harmful chemicals with safer alternatives when possible.
Noise-Induced Hearing Loss (NIHL)
Prolonged exposure to loud noise in workplaces such as construction sites, factories and music venues can lead to permanent hearing damage. NIHL often develops gradually, making it difficult to detect until hearing loss is noticeable. Once hearing is damaged, it cannot be restored.
How to avoid it:
Provide and enforce the use of hearing protection, such as earplugs or earmuffs, in high-noise environments.
Monitor noise levels and implement sound-reducing measures, such as acoustic barriers or quieter machinery.
Schedule regular hearing tests for employees working in noisy conditions.
Limit exposure by rotating staff between quieter and louder tasks.
Encourage employees to take breaks in quieter areas to reduce continuous exposure.
Burns
Burn injuries can occur due to contact with hot surfaces, steam, chemicals, or electrical sources. Workers in kitchens, factories, laboratories and workshops face a higher risk of burns, which can range from minor blisters to severe tissue damage.
How to avoid them:
Use PPE such as heat-resistant gloves, face shields and protective clothing when handling hot equipment or chemicals.
Clearly label hot surfaces and hazardous materials.
Follow proper procedures for handling and storing chemicals to prevent accidental spills or reactions.
Train employees on safe working practices and first aid measures for burns.
Keep fire extinguishers and emergency washing stations accessible.
Eye Injuries
Eye injuries can result from flying debris, chemical splashes, or prolonged exposure to bright screens. These injuries range from minor irritation to severe damage that can lead to vision loss. Industries such as construction, manufacturing and laboratories pose a higher risk due to airborne particles and hazardous substances.
How to avoid them:
Wear safety goggles or face shields when working with hazardous materials, power tools, or machinery that generates debris.
Use protective screens or barriers to prevent dust and particles from reaching the eyes.
Follow proper chemical handling procedures and store hazardous substances securely.
Take regular breaks when working on screens to reduce eye strain and dryness.
Ensure emergency eye wash stations are available and accessible in high-risk areas.
Electrical Injuries
Electrical injuries can occur due to contact with faulty wiring, exposed electrical components, or working near power sources. Shocks and burns from electricity can be severe, leading to nerve damage, internal injuries, or even fatal electrocution.
How to avoid them:
Conduct regular inspections and maintenance of electrical systems to identify and fix faults.
Train employees on safe handling of electrical equipment and emergency procedures.
Use insulated tools and wear appropriate PPE, such as rubber gloves, when working with electricity.
Ensure electrical installations meet safety standards and are properly grounded.
Never overload sockets or use damaged electrical cables.
Label high-voltage areas and restrict access to authorised personnel only
Seek Legal Guidance
If you have sustained a workplace injury, speaking to a legal professional can help you understand your rights and options. Workplace injuries can have lasting effects on your health, income and overall quality of life. A workplace injury solicitor can assess whether your employer has fulfilled their responsibility to provide a safe working environment.
Legal advice can also help you navigate the claims process, including securing compensation for medical costs and lost earnings. A solicitor can address your concerns and guide you through the necessary steps to resolve the issue.