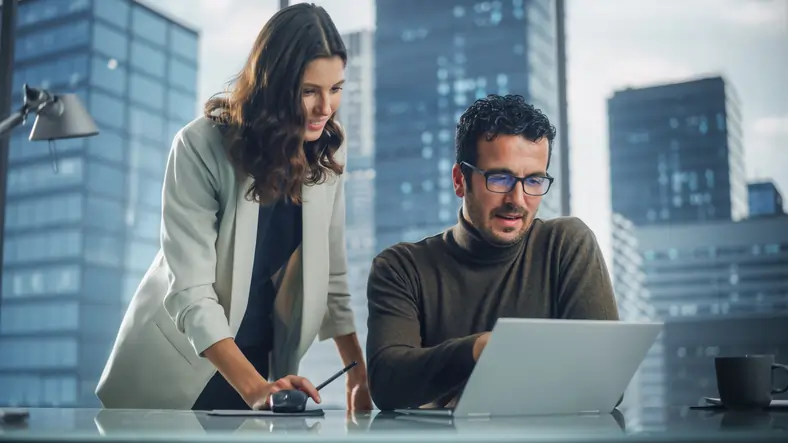
Keeping track of business equipment can be more challenging than it may seem. Whether it’s laptops, machinery, or essential tools, losing track of these assets can lead to costly setbacks and frustrations. But with the proper practices, you can account for all your equipment, saving time, money, and a whole lot of headaches.
This article shares practical tips and strategies to help you maintain a clear and organised inventory. Read on for seven best practices for tracking your business equipment!
- Leverage Data Plates And Barcodes
Data plates and barcodes serve as permanent digital identification number for your equipment. They streamline equipment tracking and management, making it easy to identify each item quickly.
When looking for these asset tags, choose robust data plates from a reliable supplier, such as MPC, that can withstand your work environment’s challenges. You want them to remain legible whether exposed to heat, moisture, or heavy use.
QR codes are also becoming more popular, and for a good reason. They offer advanced solutions, storing more information in a compact format. A quick smartphone scan reveals detailed data like purchase dates and equipment maintenance history.
This identification and labelling system benefits organisations of all sizes. From small workshops to large warehouses, smart tags eliminate guesswork about equipment status and history. They provide instant access to crucial information, streamlining and improving operational efficiency.
- Conduct Regular Audits
Regular audits keep your equipment in check and your records accurate. How often? It depends on your needs. A busy restaurant might check monthly, while a small office could do quarterly reviews.
During these check-ups, you’ll make sure everything’s where it should be and working smoothly. It’s like a health check-up for your physical assets. You might find that your printer needs new ink or discover that expensive drill you thought was lost.
But these audits aren’t just about counting stuff; they’re your chance to update your equipment tracking system and plan. For instance, you may notice that the delivery van needs a tune-up soon. This will help you avoid surprises and keep your operations running.
- Implement Check-In/Check-Out Procedures
Implement a check-in/check-out system to keep track of your equipment. This approach works like a library for your tools, ensuring you always know their location and user.
The process is straightforward: team members check out items when they need them and check in upon return. And what better method to use if you’re in a dynamic environment where equipment moves frequently?
Take a bustling photography studio, for example. With this equipment tracking software in place, the manager will know if the high-end camera is at a client’s location for a shoot or back in the editing room. It eliminates confusion and reduces time wasted searching for equipment.
Modern tracking systems streamline this process. Users can log equipment moves quickly, often directly from their smartphones. This creates a clear, real-time record of equipment usage and location.
- Track Equipment Usage
Ever wonder which tools are champions and which are just collecting dust? Tracking equipment usage gives you the inside story. It basically tracks your tools’ fitness.
You can keep tabs on how often and how long your team uses each item. You might discover that your fancy new gadget isn’t performing well while your old reliable machine is working overtime.
This knowledge is invaluable for better decision-making. It could mean buying more of your most-used items or selling those that rarely see action. The result? Reduced business expenses and improved efficiency.
- Leverage Cloud-Based Solutions
Cloud-based systems take your equipment inventory tracking to new heights. They offer perks that old-school methods can’t match.
Imagine checking your inventory while sipping coffee at home or updating stock levels right from the warehouse floor. That’s the power of cloud accessibility. You’re not tied to a single computer anymore!
These management systems keep everyone on the same page with real-time information. They eliminate confusion about what’s in stock or where items are located.
As your business grows, your cloud system grows with you. You can add more users, more items, or more features without breaking a sweat.
And the best part? Many cloud solutions come with handy extras like mobile apps and automatic updates. They make tracking your tools easier than ever.
- Train Your Team
Your asset system’s effectiveness depends on your team’s expertise. Ensure everyone who handles office equipment masters your new equipment management software, from new hires to experienced staff.
Teach the essentials – data entry, location updates, and issue reporting. Create a quick reference guide. Think of it as a cheat sheet for smooth operations. You could even design an eye-catching poster for the break room.
But don’t limit training to a non-time event. Regular refreshers keep skills sharp and reinforce the importance of accurate asset tracking. Consider hosting a monthly tracking day to share tips and address questions.
Investing in comprehensive training equips your team with the knowledge to maintain an accurate, up-to-date equipment inventory. This minimises errors, streamlines workflows, and ensures everyone can locate equipment when needed.
- Implement Digital Asset Management Software
Ditch the old-school method and embrace a digital revolution in asset management. These savvy systems take how you track your equipment to newer, higher heights. You’ll know where everything is and who’s using it in real-time. Plus, you can plan maintenance and anticipate replacements before issues arise.
When choosing a digital asset management system, go for one that’s easy to use and can adapt as you grow. A lot of asset management tools offer mobile options, letting your team update information on the spot.
This tech saves time and boosts operational efficiency. No more hunting for that one tool or wondering when the printer needs service – everything is at your fingertips!
Conclusion
Keeping track of your business equipment is essential to ensure a smooth operation, reduce costs, and maintain efficiency. By implementing these best practices, you can maintain accurate records, reduce losses, and ensure your equipment is always in the right place at the right time. A well-organised workspace where equipment is easily located and properly maintained can enhance the overall productivity and efficiency of your operations.