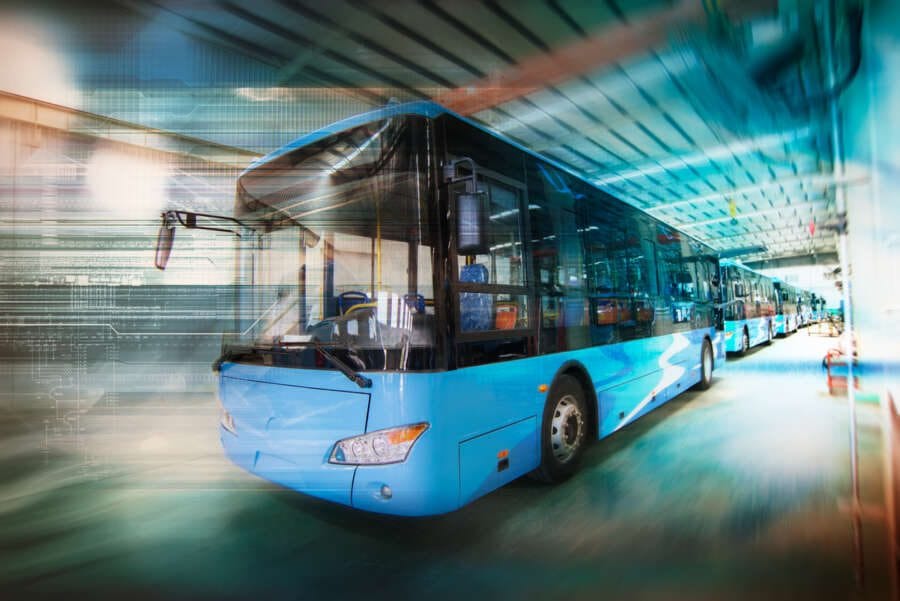
With recent advancements in technology, transport companies can now track and closely monitor the health status of their vehicles in a way they could not previously.
The overarching goal for many public transport organisations is to improve the overall on-road performance of their vehicles. This includes reducing service downtime as well as extending the lifecycle of these vehicles. Many public transport providers have implemented a number of different changes, including introducing service route changes as well as the addition of express services, all with the view of optimising operations and improving their bottom line. Whilst these strategies have worked to a certain extent, they still fell short of addressing the main pain point of these public transportation companies – vehicle service downtimes and breakdowns. These are two of the most prevalent causes of revenue loss.
Vehicle downtime – hiding in plain sight
Downtime is incredibly costly for public transport service providers, especially when caused by unforeseen vehicle breakdowns that cause unnecessary delays to passenger journeys. This hits organisations on three fronts – reduced revenue due to lack of service, hefty emergency repair bills, and reputation damage due to its association with unreliability – which also equals to a loss in revenue.
The issue of service downtime brought on by technical problems such as vehicle breakdowns has always been a pain point for many transport companies and, with the added disruption the COVID-19 pandemic has caused, many organisations are now looking at ways to revamp their services and future proof their operations.
Many are looking towards a greener future with heavy investment in low carbon and zero emission vehicles. Whilst these sustainability initiatives may seem costly at first glance simply due to the significant capital outlay that comes with both electric vehicles and infrastructure, it’s the overall operational costs and environmental impact that is driving the need for the switch to electric vehicles. In fact, electric vehicles are already estimated to have lower operating costs than fuel transmission vehicles.
However, whilst this may potentially have a positive impact for transport organisations, it still does little in tackling the age-old issue of dealing with vehicle breakdowns and reducing service downtime.
Current issues and practices
For many transportation companies, the upkeep of their fleet of vehicles is an expensive affair which makes vehicle breakdowns a major cause for concern. Reason for this is the higher cost of emergency repairs that come with such incidents which often entail recalling a vehicle off the road and paying for parts that need to be delivered at short notice – all of which rack up a substantial workshop bill.
From an image perspective, downtime also causes the type of service disruptions that, in the long term, undermine the passengers’ confidence in the reliability of a bus route, or even the entire service network. This, in turn, impacts revenue generation, as customers are less incentivised to use public transport services they deem inefficient. The result is a ripple effect of revenue loss and increased spending, which ultimately affects transport operators’ bottom line.
In an effort to tackle the issue of downtime and reduce such incidences altogether, transport service companies have tried and settled with a number of different remedial processes including planned downtime and regular service check-ups in an effort to remain on the front foot and minimise the impact of vehicle breakdowns. This has often resulted in muted improvements, falling short of the zero downtime outcomes that many were looking to achieve.
Leveraging the power of technology to tackle breakdowns and downtime
Vehicle downtime is an issue generally caused by the breakdown of vehicles that typically stems from the company’s fleet maintenance department lacking the tools to detect and deal with the issue proactively. This is where the use of next-generation technology can help not only to minimise the frequency of these costly breakdowns, but to also eliminate them completely over time. Technological solutions such as Artificial Intelligence (AI) powered predictive maintenance can help companies monitor the health and status of each vehicle component in real time, offering actionable intelligence to plan maintenance operations.
The plethora of data intelligence gathered from these vehicles can be used effectively by public transport companies to monitor to monitor anything from simple parameters such as fuel levels to more complex State of Health of major vehicle components, we well as wear and tear of parts, enabling them to act accordingly and in a timely manner, addressing specific issues before the vehicles hit the road.
Major transport network companies such as Go-Ahead Ireland (GAI) are already utilising next-gen technology in the shape of AI-powered real-time predictive fleet maintenance solutions to anticipate and prevent unexpected vehicle breakdowns and the service downtime that comes with it. More interestingly, GAI managed to extend the use of this technology to its entire fleet with expected reduction in vehicle breakdowns by over 57% in the next three years.
The unique thing about AI predictive maintenance tools is their ability to enable transport companies to effectively reduce vehicle unexpected breakdowns by turning actual vehicle data into useful intelligence that can be used to inform and optimise maintenance operations. This plethora of readily available data points on vehicle conditions are collected and analysed by the AI platform, which turns them into real-time actionable insights that allow transport companies to predict and proactively deal with potential vehicle breakdowns and as a result completely eliminate the issue of downtime.
With a new dawn in digital innovations thanks to the emergence of next-gen technology, transport companies no longer have to rely on feeble mileage-based estimates when it comes to monitoring their vehicle health. They can now adopt tech solutions that can help them to reduce the frequency of preventive checks and plan the wear rate of components dynamically. This ultimately will help companies to not only offer a more reliable service to passengers, but to save money and resources too.